Managing a fleet with a diverse range of vehicles can be challenging, which is why having a strategy for acquiring special-purpose vehicles is essential. We speak to two experts who outline their fleet management processes.
Organisations that utilise vehicle fleets generally have multiple reasons why the fleet exists, which translates into the need to maintain a variety of vehicle assets.
Most of these assets consist of standard makes and models across a range of asset classes, such as light and heavy vehicles, including asset types such as sedans, SUVs, utilities, light trucks and heavy trucks to name a few. User requirements sometimes outstrip manufacturer’s offerings, however, which necessitates re-engineering aspects of a vehicle – typically the body – and then applying enhancements to make them fit-for-purpose.
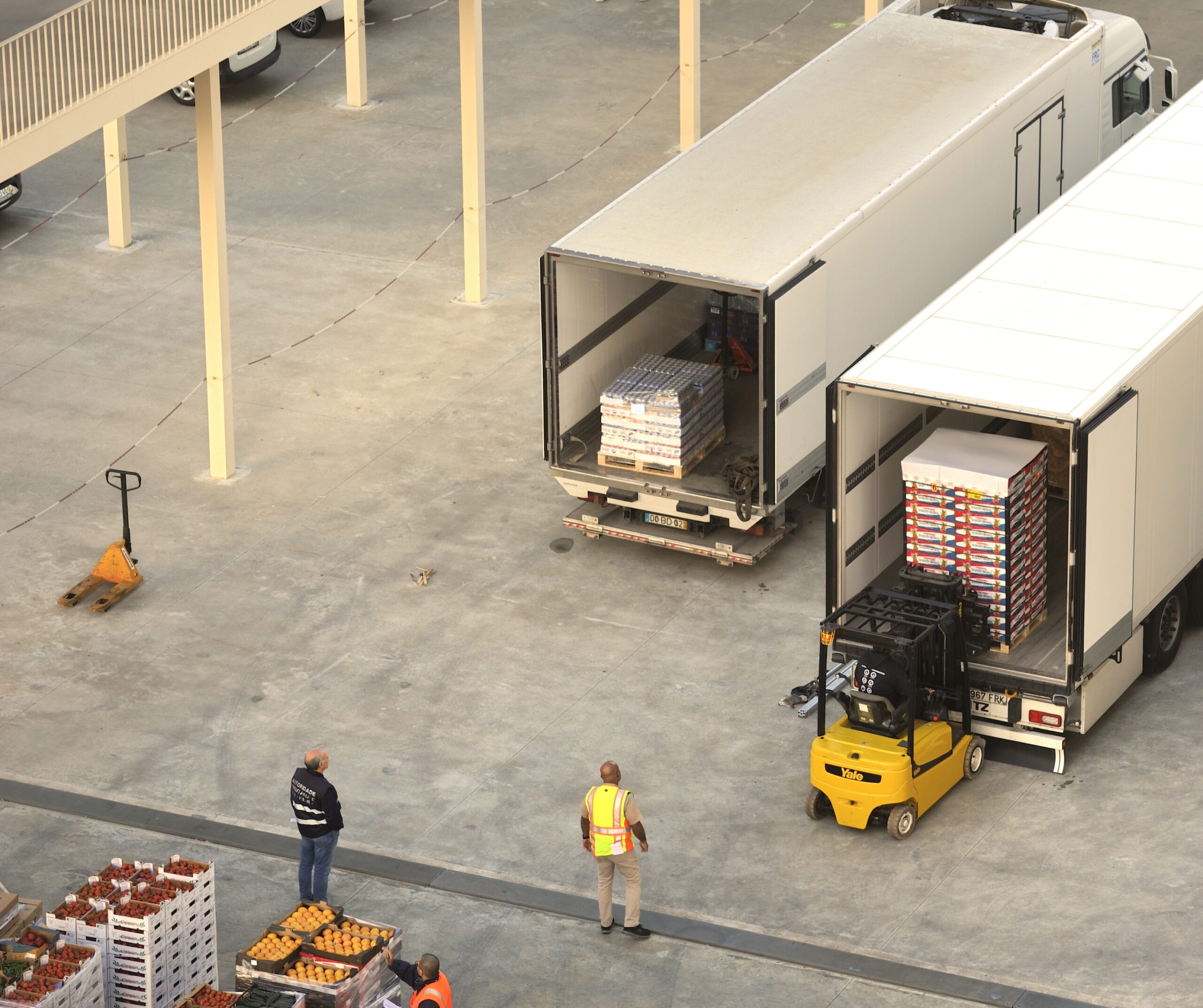
IPWEA explored this special-purpose acquisition process when we held the third of our Fleet Winter Webinar 2020 series. The session broke down the process, from defining user needs and developing a clear vision to specification considerations and finalisation.
Designing a special-purpose vehicle plan
The importance of having a defined process is the key to successfully acquiring a special-purpose vehicle (SPV), insists Dan Fischer, Senior Engineer with the Hidrive Group.
“Any supplier you deal with should have a process,” he says. “Some may have more steps and some may have less… [and] the more work you can put in at the start of the process the better things will go.”
Fischer says the main steps should include:
- Understand requirements
- Review compliance (e.g. regulations, standards, etc.)
- Consider product fit
- Model the build (e.g. computer-aided design)
- Collaborate during idea iterations
- Establish a source of truth for the design
- Schedule the order
- Optimise the manufacturing process using engineering services
- Ensure quality checks during production, and
- Conduct final QA and testing prior to sign-off and delivery.
From a fleet practitioner’s perspective, the process has more steps. City of Gold Coast’s Acting Heavy Vehicle Management Officer, Kris Browne, says the stakeholder’s SPV acquisition process starts sooner than the suppliers process at the point of replacement identification.
“I request our proposed Replacement Plan early so I can start the process of contacting each user area and notify them when their vehicles are due for replacement,” he explains.
The SPV acquisition process then ends later with a procedure to decommission and auction the SPV. In fact, the beginning and end points are reflective of a standard procurement and disposal process. The steps in between create more complexity when acquiring special-purpose vehicles.
Creating a special-purpose vehicle specification
A critical part of the SPV acquisition process is ensuring that the vehicle will be fit-for-purpose while balancing and managing expenditure, taking into account that, “if a driver had it his or her own way, they would spec the most customised truck body design”, says Browne.
Based on this dilemma, he believes standardisation helps resolve the issue. “We need to get the best financial deal for the city, so we’ve standardised each branch vehicle so we can determine how much the replacement will cost,” he says, acknowledging that, “each user area has their own fit-for-purpose, standardised body layout”.
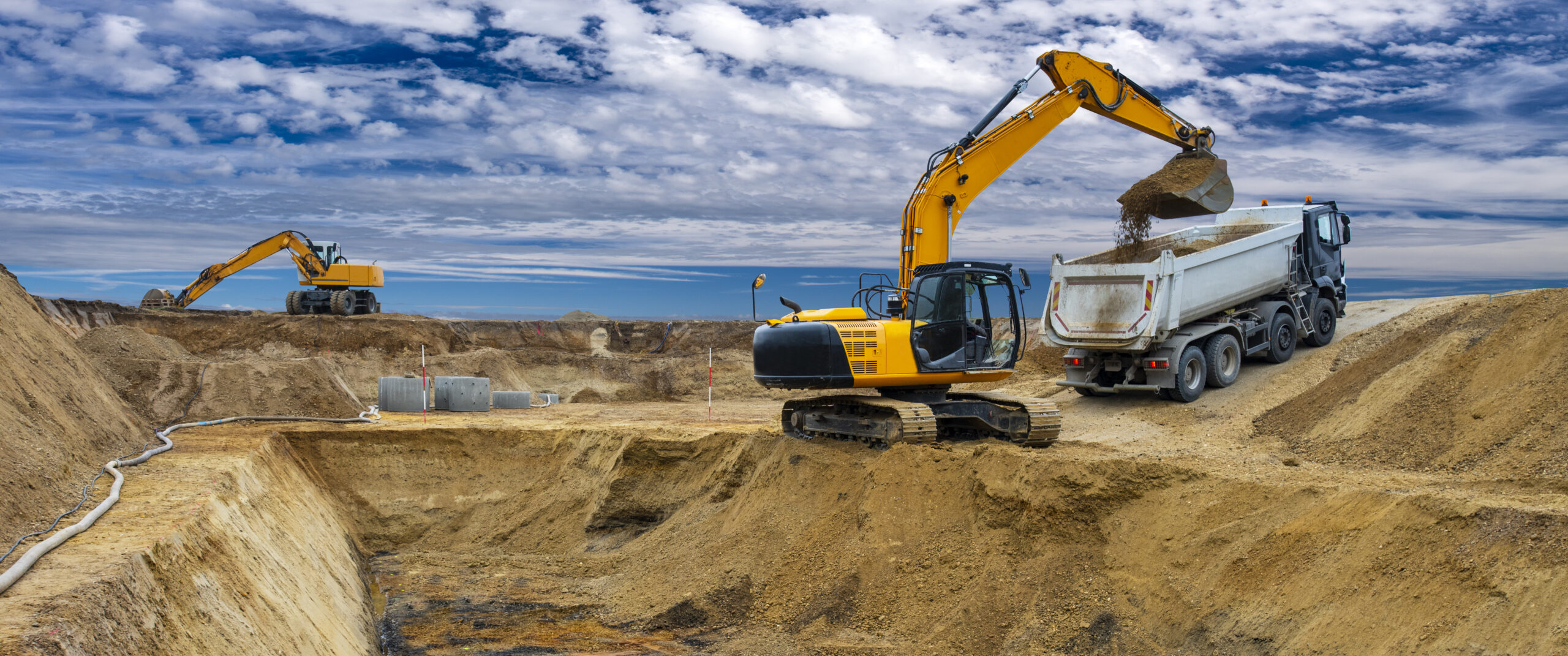
There are a number of points to consider when creating a suitable SPV specification. Says Browne: “Without a doubt the essential specifications are safety and ergonomics.” However, there are other areas to consider as well, including:
- Body layout and possibly multiple layouts to provide choice
- Location of tools and emergency equipment
- Body and cab chassis weight
- Tie-down points
- Vehicle size to suit location access and terrain
- Safety features for active/reactive driving
- Ergonomics (e.g. ingress/egress, suspension, height, etc.).
Realising a fleet management strategy
In summary, acquiring special-purpose vehicles should be a structured, process-driven exercise to ensure the right outcomes. It requires understanding what the organisational requirements are and enhancing the right vehicles to closely match those needs while balancing the organisation’s budgetary constraints.
This requires numerous parties to work closely together, including stakeholder user groups and crews, fleet practitioners, the executive team, and trusted supplier teams that assist the stakeholder through the process. This is coupled with a standard procurement and disposal process when timing for replacement of SPV’s has been identified.