By: Dr. Jacqueline Balston, Director of Sustainability, IPWEA
Context
Steel is widely used in a diverse range of infrastructure due to its relatively low cost, high strength-to-weight ratio, conductivity and malleability. In buildings steel is used in structural sections, reinforcing bars, sheet products such as roofing, purlins, internal walls, ceilings, cladding and insulating panels for exterior walls, non-structural steel and internal fixtures1. For infrastructure, steel is used in bridges, tunnels, rail track and in buildings such as fuel stations, train stations, ports and airports, water and gas pipes1.
In 2020 global steel production was about two billion tonnes2. For each tonne of steel produced in the conventional blast furnace-basic oxygen furnace process, between 1.5 and 3 tonnes of fossil carbon are released into the atmosphere2. As a result, steel production generates approximately 7% – 8% of global greenhouse gas emissions2,3. To meet the Paris Agreement commitments, steel process emissions must fall by at least 30% by 2030 to bring the sector in line with a 2050 net-zero target2.
Greenhouse gasses are emitted in the traditional production of steel from two sources. First, to create pure (pig) iron from iron ore requires oxygen bonds in the ore to be broken. When coal is used as a reagent the chemical reaction releases CO2 as a bi-product4. In addition, the process of forming the iron into steel of useful shapes requires high temperatures in a blast furnace usually generated from fossil fuels4.
Research has been underway for a number of years to develop lower emissions “green steel” technologies that do not require fossil fuels in the process. However, despite these technologies, the process of creating new steel will continue to demand extremely high levels of energy, and if the grid used to provide the energy is not from renewable resources, the emission can be higher than using old technologies4.
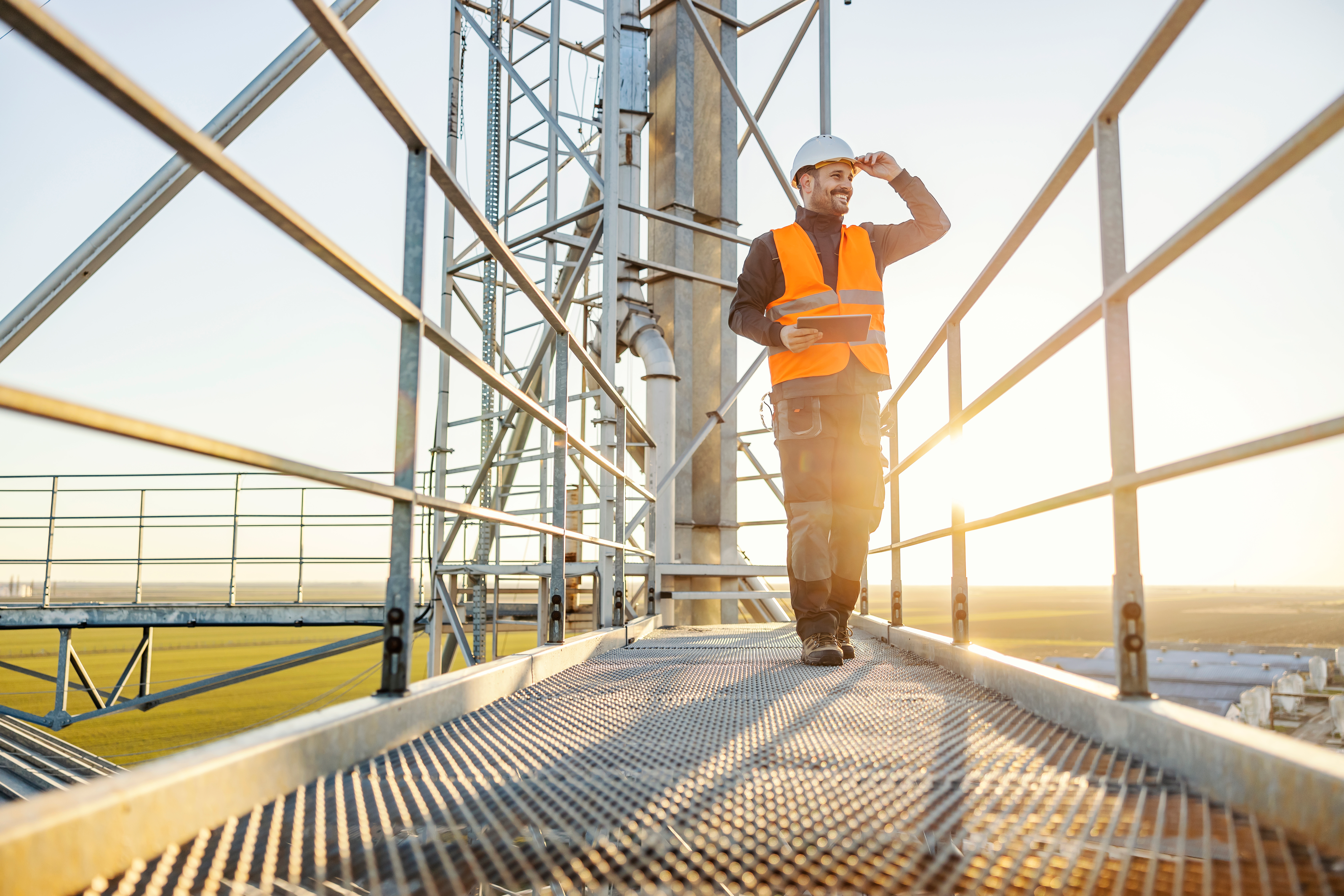
Maintenance of existing stock
The most sustainable option available to asset managers is to extend the useful life of existing steel structures by improving maintenance, refurbishing old stock and protecting assets from changes in the climate.
Practice Note 12.1: Climate change impacts on the useful life of infrastructure, was published by IPWEA in 2019 and describes the likely impacts of climate change on steel infrastructure including changes to steel and zinc corrosion rates, excessive expansion that may buckle railway lines or cause power cables to sag, and increased stresses from drying soils, extreme winds or bushfire events. A simple decision tree methodology for determining the likely change to asset useful life is provided and estimates of useful life for over 200 assets is given7.
The follow-up publication Practice Note 12.2: Climate Resilient Materials for Infrastructure Assets released in 2021 provides an extensive range of options to reduce the impact of climate change and extend asset useful life8. Options to increase the asset life of steel components include changes to maintenance schedules, strengthening existing members or applying protective coatings such as epoxy, fibre reinforced polymer or polyurethane paint, hot dipped galvanising, intumescent paints or fire-rated boards7,8.
Climate smart design
The placement, orientation and treatment of steel components have the potential to dramatically increase the useful life of new assets. External steel elements should be designed and orientated so that water drains away and does not pool8. The selection of fixings, steel protection, waterproofing layers and cladding materials should also be carefully considered, particularly in external environments.
Galvanic corrosion can occur as a result of dissimilar metals coming into contact with each other in the presence of an electrolyte (e.g. water from the atmosphere) 8. As a result it is important to select similar metals (with minimal electrical potential difference between them) or to ensure that metals are properly isolated from each other8. Fixing points are prone to corrosion and can lead to rapid degradation of materials under some conditions8.
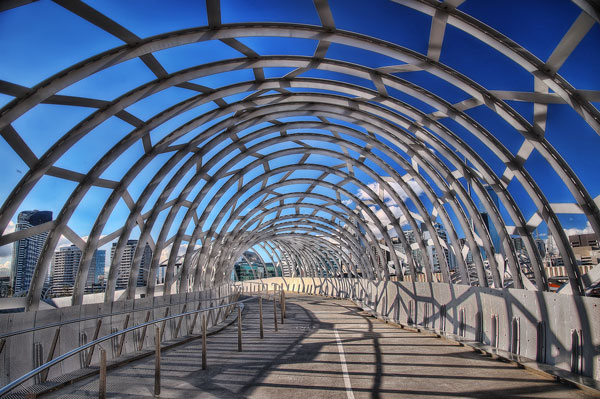
Recycled steel
If properly maintained, steel can be stripped back, cleaned and reused without the need for recycling. But if new steel is required, consider using recycled material. In 2019 about 22% of globally produced steel was made by re-melting scrap in an electric arc furnace2. But the full potential of reused and recycled steel is currently unfulfilled2. Be aware that recycled steel tends to be of lower quality, due to poor sorting and contamination issues and so more research is underway to improve recycling processes2.
Green Steel
The two most promising low-carbon technologies for steel making are hydrogen direct reduction (HDR) and molten oxide electrolysis (MOE)4.
In the case of HDR, hydrogen is produced using green energy and then used to generate the heat required to make pellets of solid iron from iron oxide without coal. The iron pellets are then heated to a point where the molten steel can be transformed and shaped inside an electric arc furnace3,4. In late 2020 the world’s first fossil free steel was produced by HyBRIT in Sweden using the HDR method. By 2025 they plan to produce fossil free iron ore pellets for the first time on a large scale9.
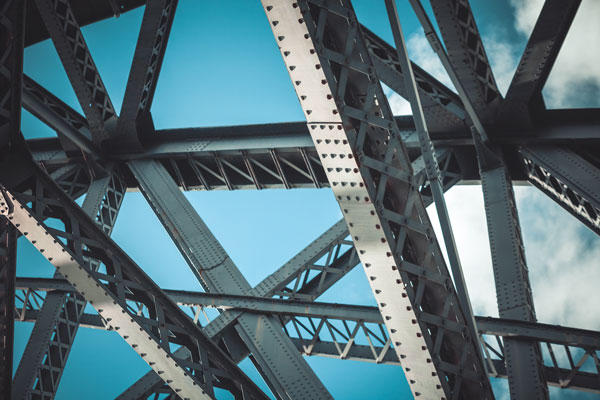
With MOE the process starts with iron ore and goes directly to liquid metal ready for shaping, rolling or casting in one step without using coal, hydrogen or a blast furnace4. For this reason it is considered by some to be a more efficient process5.
To date, seven out of the ten biggest steel producing countries have initiated at least one green steel project2. In Australia, Fortescue Metals in the Pilbara and Liberty Steel Australia at Whyalla have both announced full scale green steel production by 2023/242, and BlueScope Steel and Rio Tinto have agreed to begin exploring methods of decarbonising the steel-making process6. Overseas, national and local governments (including those of Germany, the Netherlands, California and South Africa) have included green steel in their public procurement policies2.
The embodied carbon of Australian made virgin Steel is 5 kgCO2/kg. For 85% recycled steel, this reduces to 2.8 kgCO2/kg8. Current best practice use of steel would be to maintain and potentially extend the useful life of existing infrastructure, use recycled steel where possible and finally to purchase green steel from an Australian supplier when available8.
For further information please access a copy of Practice Notes 12.1 and 12.2 on the IPWEA website at: www.ipwea.org/pn12-2
References
1. World Steel Association (2022), Steel in buildings and infrastructure. Accessed 23 February 2022 at https://worldsteel.org/steel-by-topic/steel-markets/buildings-and-infrastructure/.
2. World Steel Association (2021), Global crude steel output decreases by 0.9% in 2020. Accessed 23 March 2022 at https://worldsteel.org/media-centre/press-releases/2021/global-crude-steel-output-decreases-by-0-9-in-2020/
3. Leadit – Leadership Group for Industry Transition (2022), Green steel production: How G7 countries can help change the global landscape. Accessed 23 March 2022. https://www.industrytransition.org/insights/g7-green-steel-production/
4. Rocky Mountain Institute (2019), The disruptive potential of Green Steel. Accessed 23 February 2022 at https://rmi.org/wp-content/uploads/2019/09/green-steel-insight-brief.pdf
5. ABC News (2022), Startup promises green steel by 2025 as decarbonisation race heats up. Accessed on 23 March 2022 at: https://www.abc.net.au/news/2022-02-08/startup-promises-green-steel-by-2025/100811450
6. ABC News (2022I, BlueScope Steel and Rio Tinto join forces to investigate ‘green steel’. Accessed on 23 March 2022 at: https://www.abc.net.au/news/2021-10-29/bluescope-and-rio-tinto-enter-green-steel-partnership/100580922
7. IPWEA (2019), Practice Note 12.1: Climate change impacts on the useful life of infrastructure. Institute of Public Works Engineering Australasia, Sydney, Australia. Accessed 5 February 2022 at https://www.ipwea.org/publications/ipweabookshop/pn12-1
8. IPWEA (2021), Practice Note 12.2: Climate Resilient Materials for Infrastructure Assets. Institute of Public Works Engineering Australasia, Sydney, Australia. Accessed 5 February 2022 at https://www.ipwea.org/publications/ipweabookshop/pn12-2
9. HyBRIT Fossil Fuel free Steel (2022), A fossil free future. Accessed 23 March 2022 at https://www.hybritdevelopment.se/en/a-fossil-free-future/