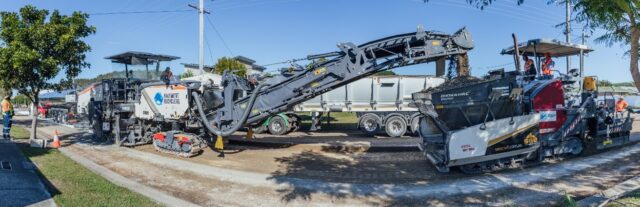
The public works sector is increasingly recognising that the path towards excellence and simply ‘doing things better’ is marked by three guideposts – environmental, social and economic outcomes. In the realm of roads, one contractor has been creating opportunities with a back-to-basics approach and a vision of a more sustainable future.
Stabilisation techniques are fundamental, yet demonstrate the biggest pavement recycling impact through simply rehabilitating the existing road pavement materials in situ. Techniques are founded on geotechnical engineering principles and focus on the critical structural layers within a pavement. Therefore when properly conducted, these recycling solutions offer road asset managers long term results lasting decades, rather than various resurfacing options that address the top layers only.
Recycling through stabilisation has been traditionally preferred amongst road asset managers due to offering competitive direct costs and fast construction, which are achieved by efficient resource utilisation when compared to equivalently designed, conventional dig-out-and-replacement methods.
Stabilised Pavements of Australia is an Australian-owned company that has become the largest specialist stabilisation contractor in Australasia. Starting in Australia in 1984, the company has since expanded overseas to operate internationally.
In early 2020, the company launched a new division called Pavement Recyclers – one of the most major developments in the company’s 37 year history.
Pavement Recyclers specialise in delivering Paver Laid In Situ Recycling. This involves a single-pass, paver-laid process to recycle pavements in a forward moving train. State-of-the-art technology is used to rehabilitate the existing road pavement materials onsite. All operations occur in just one pass of the forward moving train including milling, recycling, material management and placement. Alongside many improved features on current conventions, the single-pass, paver-laid aspect is a key difference compared to other recycling methods in Australia.
Pavement recycling of this kind is only possible using specialised machinery – the Wirtgen 380 Cold Recycler from Germany. There are limited numbers of these recyclers available worldwide, and importing the first into Australia has meant keeping the country at the forefront of industry innovation.
The recycler machine showcases a full working width of 3.8 metres, with the paver screed capable of extending even further. Depending on the project, this allows recycling to occur in a single pass across full lane widths, multiple lanes or with simultaneous shoulder widening. The machine also doubles up as the world’s largest profiler.
If introducing a process and machinery never-before-seen in the country wasn’t enough, the initiative sparked a golden opportunity to take the company’s passion for recycling roads a step further.
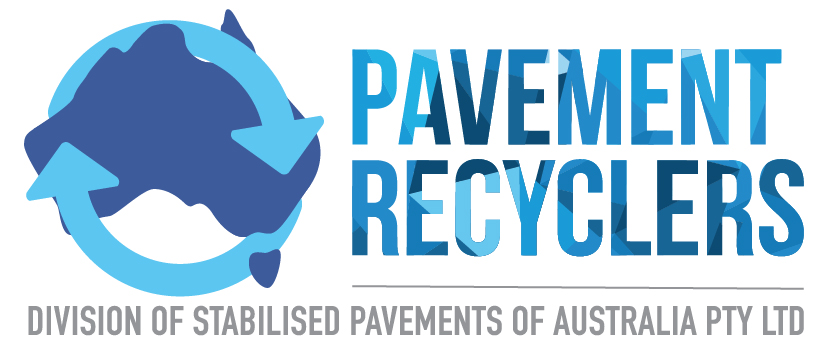
The move to headline the division with the new ‘Pavement Recyclers’ brand and logo aims to highlight the core function of the service. Whilst there have been creative concepts to increase the use of recycled materials in roads, Pavement Recyclers are centered on maximising the recycling potential of the most obvious, yet often overlooked, resource – the existing road.
Beyond direct road rehabilitation services, Pavement Recyclers are committed to going the extra mile with helping clients achieve their sustainability outcomes. Sustainability Reports compiled on completed projects quantitatively measure metrics that are often difficult to express tangibly, such as greenhouse gas emissions and resource utilisation.
Sustainability Reports consistently demonstrate that compared to conventional construction, Paver Laid In Situ Recycling yields 30-50% direct cost savings, lower emissions by over 60%, and recycles thousands of tonnes of material onsite.
General Manager of Pavement Recyclers, David Berg, says “It’s a single-pass process with a clean, paver-finish that recycles up to 100% of the existing pavement material. As recycling is the global direction in the industry, this process will become commonplace.”
“Asset owners have the opportunity to revolutionise the way pavements are rehabilitated. Through this technology, Pavement Recyclers can deliver pavements with structural integrity, environmental sustainability and economic savings.”
So far, the most popular type of Paver Laid In Situ Recycling treatment has been Foamed Asphalt, which uses foamed bitumen technology.
Foamed Asphalt pavements are a real display of excellence in engineering; whilst the modulus can reach high strengths to withstand heavy traffic, the pavement remains flexible and thus can be constructed at relatively thinner thicknesses.
Foaming the bitumen allows the binder to coat the fine particles and create a mortar, enabling intrinsic binding within the mixture that differs to how conventional asphalt is manufactured. The benefits of this are superior water impermeability and resistance to high temperatures in service. The design, construction and performance of these pavements are a true embodiment of sustainable infrastructure.
Foamed Asphalt is an alternative to conventional asphalt, and has been popular with authorities committed to sustainable infrastructure strategies. The first project in Australia was undertaken in partnership with Central Coast Council, followed by other state and local government authorities on the eastern seaboard.
As part of the many exciting developments in the industry, Pavement Recyclers endeavors to continue a leading role and advocate first principles in road recycling.
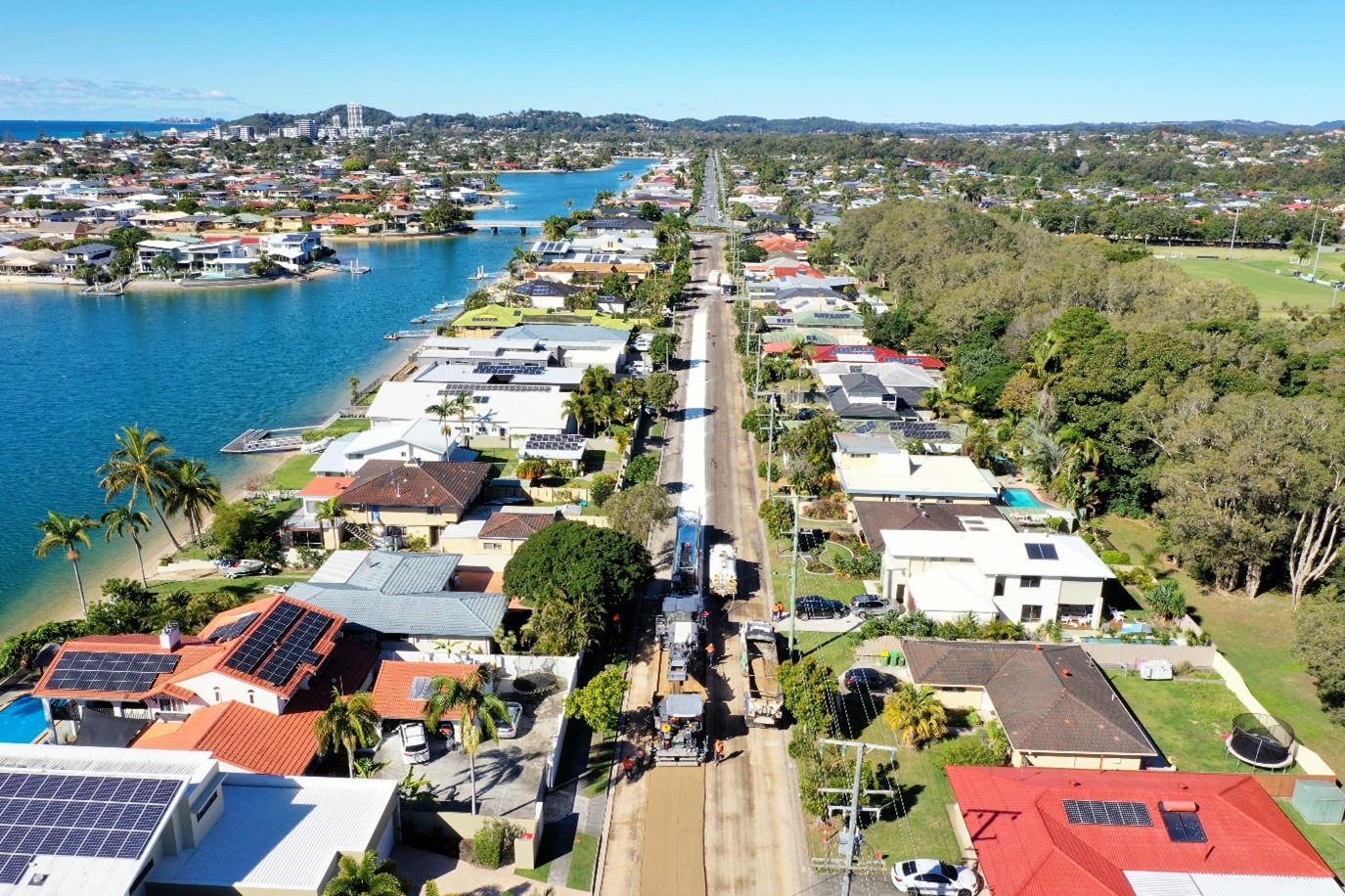