In September 2023, a corroded pole failed in high winds on the Wellington Urban Motorway. The occupants of a car, who were driving at 80km/h, were thankful that they escaped without being injured or killed after the pole crashed across their front windscreen. This terrifying incident highlights the infrequent but highly dangerous consequences of street lighting pole failures.
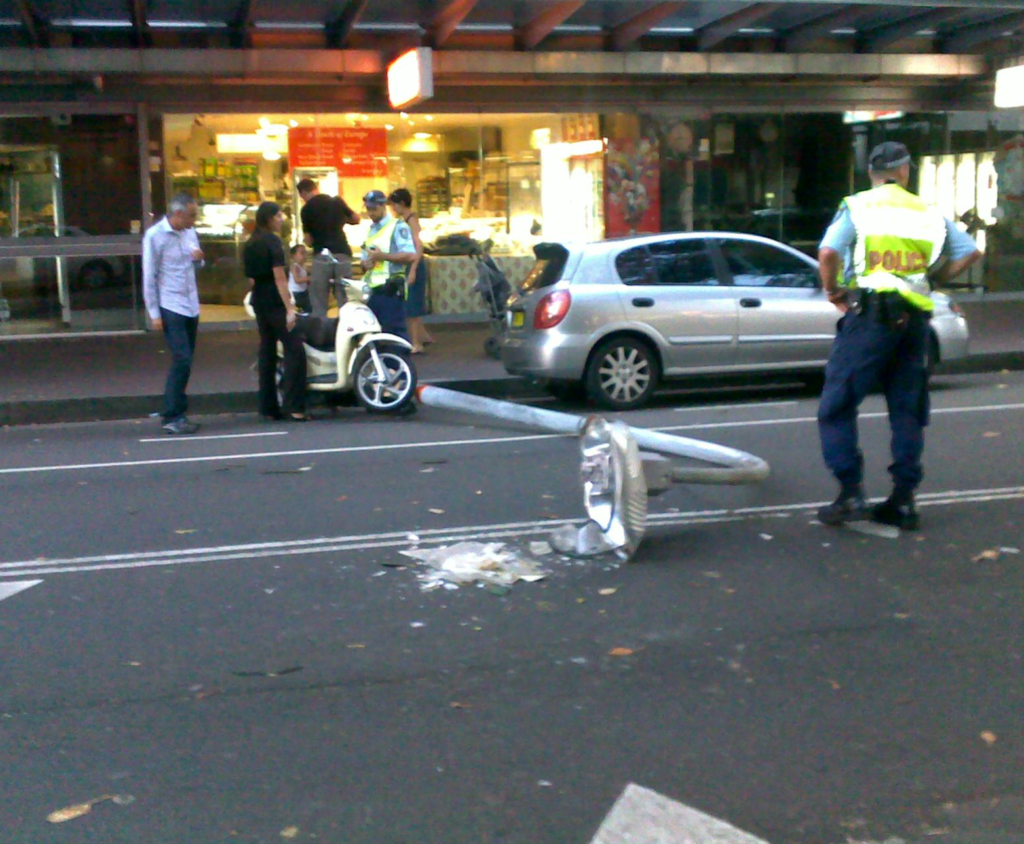
Street lighting poles are high capital cost items that are intended to have long service lives of anywhere from 25-50 years. So, how do councils, road authorities and utilities both reliably extend pole service life and prevent pole failures?
This article, which is by no means intended to constitute comprehensive engineering advice, is designed to provide a plain English introduction to the key areas of risk and outlines the elements of a typical proactive pole inspection and maintenance strategy. The article focuses on steel street lighting columns as these are owned by all three major types of street lighting asset owners across Australia and New Zealand (e.g., local councils, road authorities and utilities). Other types of poles such as wooden utility distribution poles and concrete, fibre composite and aluminium poles have similar but also unique maintenance requirements.
Risks to Poles
Some of the most common risks associated with steel street lighting poles include the following:
- Corrosion – Moisture is a big contributor to pole corrosion and often the cause of pole failures. In both Australia and New Zealand, where much of the lighting is within a few kilometers of the coast, salt exposure compounds the corrosion risk. Depending on the location, dogs and whipper snippers can also add to the challenge. Direct-buried poles siting in highly alkaline or highly basic soils can face an even higher rate of corrosion. Steet lighting poles are generally galvanised to resist corrosion, but galvanising (a form of sacrificial corrosion) only lasts for so long.
- Physical Damage – Street lighting poles are vulnerable to physical damage from vehicles, vandalism or even natural events like storms and falling trees.
- Electrical Safety – Street lighting poles contain an increasing array of electrical wiring and devices which can develop faults due to age, pole damage and environmental factors.
Elements of a Pole Inspection and Maintenance Regime
An proactive pole inspection and maintenance regime is essential to ensure that poles serve their purpose yet do not pose an undue risk to staff or the community. The key elements of a typical pole inspection and maintenance regime include some or all of the following:
- Inspection – Visual pole inspection of poles are typically undertaken on a 4-8 year cycle after a certain minimum age is reached. Conducting the first inspections after 10-15 years is common with a sampling approach sometimes used for initial inspection cycles).
The inspections are intended to identify rust, damage, loose attachments (e.g., lights, traffic signals, telco equipment, banners, signage, CCTV and many other device types), loose cladding, insecure access plates and leaning poles.
In the case of direct-buried poles, they commonly corrode near ground level. if evidence of rust is seen above ground level, partial excavation is required to assess the below-ground condition of the pole. Depending on the severity of the findings, the pole may be condemned or, in less severe but still concerning cases, the inspection frequency may be increased.
Some pole inspections go one step further in using an elevated work platform to get up the pole and manually check that any attachments and associated connections are safe and secure. - Sounding of Poles – In conjunction with visual inspections, a hammer is often used by inspectors near the base of the pole to take a sounding. After striking the pole with gentle force (so as not to damage coatings), they listen for the sound of rust falling inside the pole that has been dislodged by the sounding. This can be an indication of significant corrosion.
- Non-Destructive Testing – Various types of non-destructive testing including deformation tests and ultrasonic methods have been developed for pole testing. Some of these tests can also detect fatigue and failure in bolts where poles are mounted on footings.
- Re-coating – Some organisations apply rust converter when rust is observed on a pole (typically one that has undergone partial excavation). An epoxy coating is also regularly re-applied by some organisations on the base section of each pole.
- Electrical Inspections – There are mandatory requirements to regularly inspect, test, verify and record the condition of all electrical assets. These are established AS/NZS 3000, AS/NZS 3017, AS/NZS 2019, jurisdictional service installation rules and network standards. Poles generally require electrical inspection to ensure correct operation and safety every 5 years.
Want to learn more about pole inspection and maintenance? Most utilities in Australia publish a network standard for pole maintenance that describes their approach to inspection and maintenance. Some capital cities and road authorities have also published maintenance plans or have released tenders that contain details of their pole inspection and maintenance regimes.