
Durable, re-usable, and recyclable. Modular stainless-steel technology is helping councils save time and money while delivering sustainable, greener projects for some of Australia’s most iconic pools.
As both clients and local governments turn their eyes towards more sustainable construction practices, an emphasis on sustainable technology sets the discussion on how companies can better deliver on these expectations. What metrics are relevant to measure, what qualities are important to consider, and how do these factors figure into the broader goals of completing a project on time and on budget?
In the case of the aquatics industry, companies like Myrtha Pools are providing councils innovative solutions to reduce costs and produce greener outcomes using modular stainless-steel technology.
Embodied Energy: Why it matters and how to reduce it
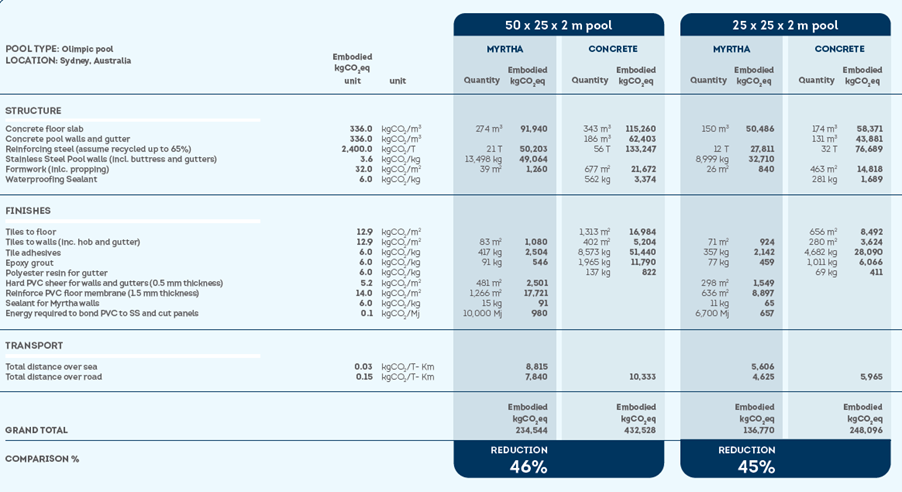
Over the lifetime of a pool, environmental impact is measured in two ways: embodied and operational emissions. Embodied emissions refer to the C02 emitted during the manufacture, transport, and construction of building materials. On the other hand, operational emissions refer to the C02 emissions related to the energy required to operate the facility during its lifetime (heating, ventilation, lighting, pool plant operation, etc.).
When compared against traditional technologies such as concrete construction, the use of modular stainless-steel technology can attribute for as much as 40% less embodied emissions for a pool build of the same size. These reductions come from a variety of factors unique to modular technology in general, and from the choice of stainless-steel as a material in particular.
Modular Design: How it works
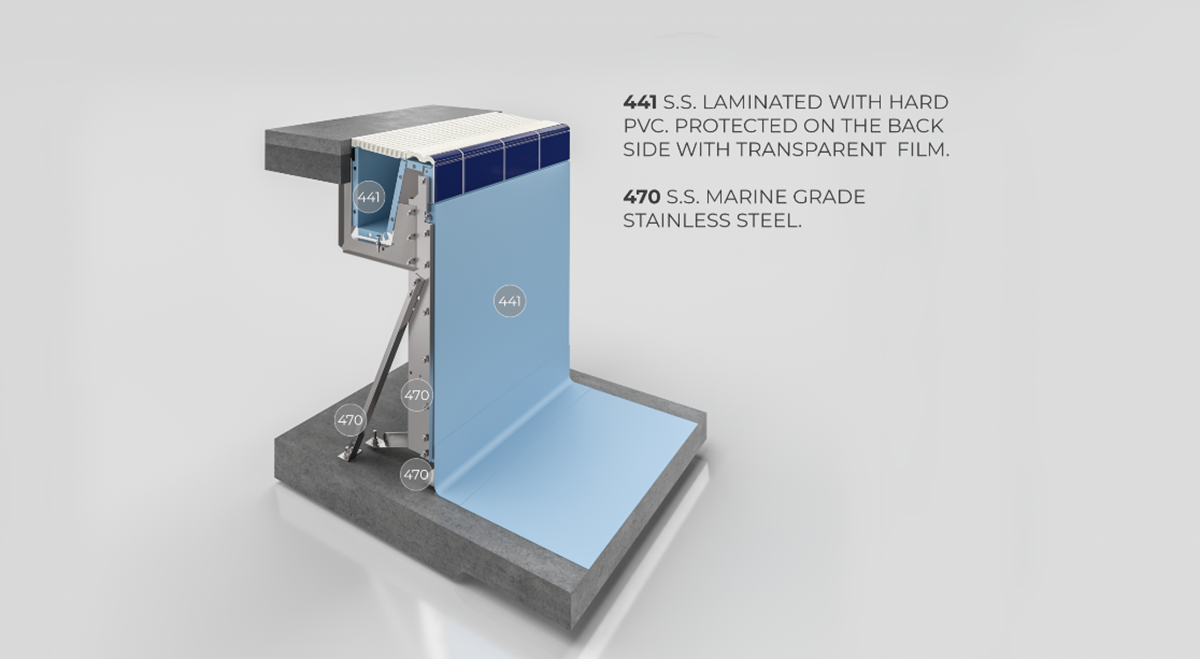
Unique to modular construction is the design for disassembly and adaptive re-use of components for a project. In terms of reducing embodied emissions, this advancement in construction not only produces less material waste but also reduces the need for heavy machinery and construction program time.
EXPLAINED: Myrtha Pool’s stainless-steel components are fully fabricated offsite and installed by a specialist installation team. Due to the pre-engineering and quality control by a single supplier and installer, the detailed coordination of pool fixings, fittings, and systems is optimized, and coordination errors are significantly reduced.
This not only practically eliminates the material waste on site, but also significantly minimizes the need for rework due to defects during construction.
Assembly can be handled by as few as two people, reducing the need for heavy machinery or cranes for assembly of the pool walls. Similarly, because the panels are assembled by piece, they can also be quickly disassembled during maintenance in the event of defects or if future upgrades are desired. These qualities drastically reduce the amount of demolition, excavation, and time required for completion compared to alternate technologies.
Greener, easier pool refurbishments
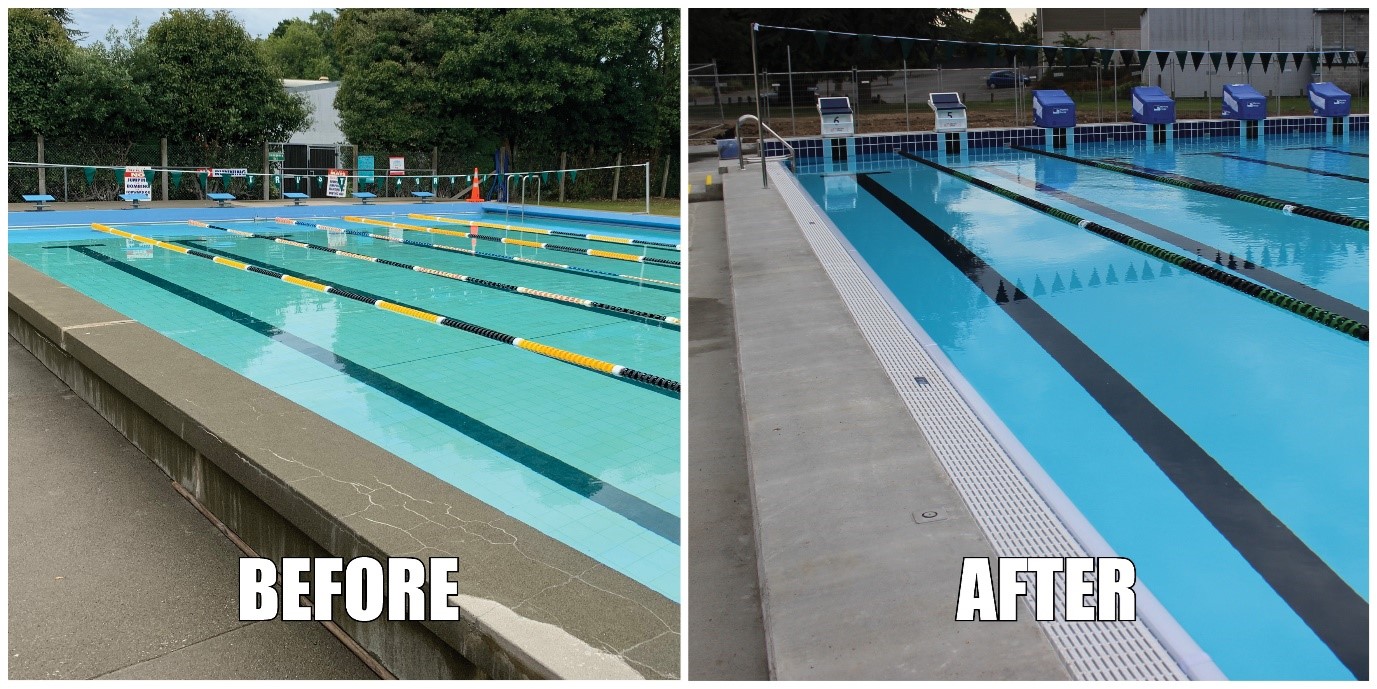
THERES MORE: On top of being used to build new pools, the same technology is also saving councils time and money by minimising demolition requirements when refurbishing their old memorial pools.
RenovAction® is Myrtha’s technology specifically developed for refurbishment and renovation of existing concrete pools. The system uses a modified modular Myrtha panel system, which acts as a new internal liner to the existing pool shell. The RenovAction® system can completely refurbish an existing concrete pool and provide water tightness guarantee, for a proportion of the cost of building a new pool, utilizing the structural integrity of the surrounding tank. The RenovAction® system can integrate the pool surround drainage system, which allows for ease of deepening of the pool to increase usage profile.
The refurbishment approach, not only provides cost savings but also significantly reduces the environmental impact of a complete rebuild project, through the following:
• Energy and waste related to demolition are significantly reduced.
• Significant reduction of material use compared to a complete re-build, resulting in reduction in CO2 emissions for the project
• Energy reduction during construction as heavy machinery or cranes are not needed for assembly.
RECYCLING
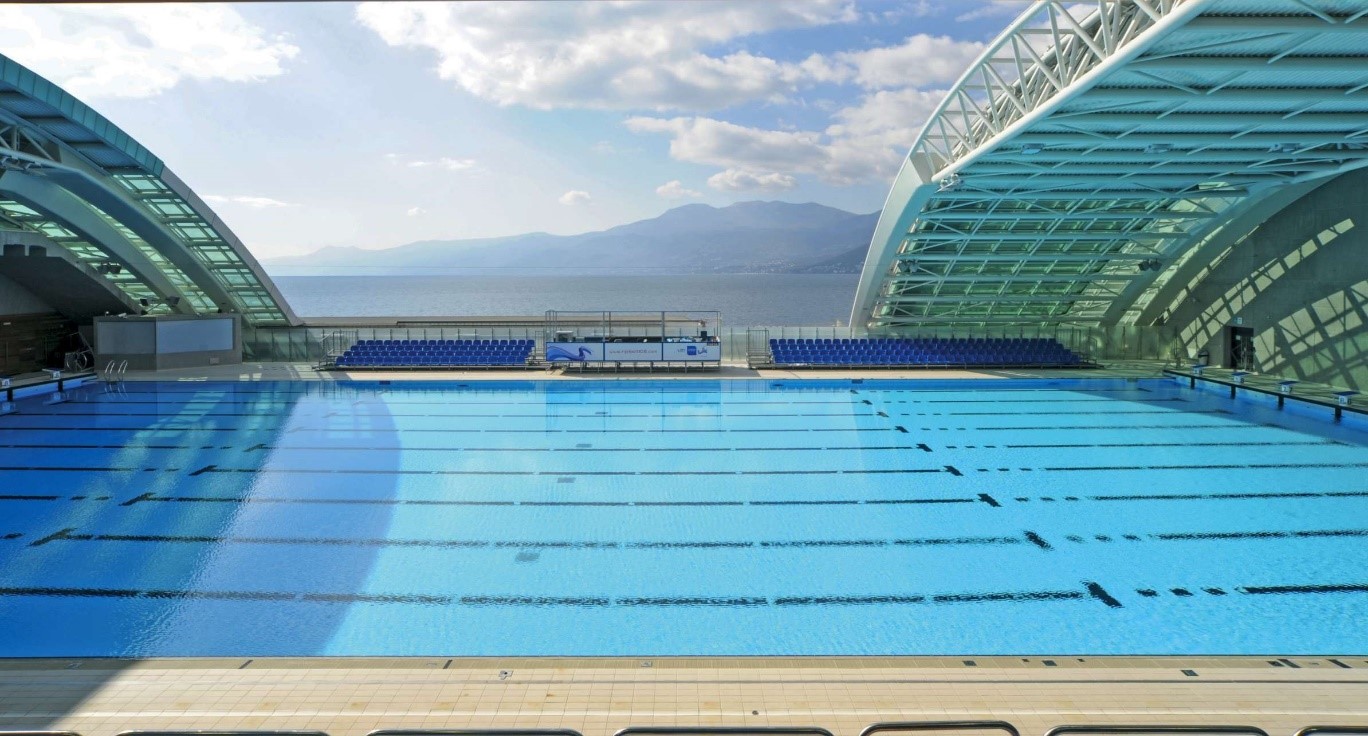
The choice of stainless-steel as a material not only provides strong durability, but also enables for better recyclability of components at the end of life. Recycling reduces the impact on the environment from the extraction and processing of virgin materials, thus reducing a project’s overall embodied energy.
Due to the inherent value of stainless-steel as scrap, and the efficiency in which it can be recycled, stainless steel recycling has been in existence for many years. The stainless steel used to fabricate the Myrtha Pools wall panels, gutters, and buttresses contain up to 65% recycled content. Additionally, the modular assembly system means that a pool can easily be disassembled at end of life, which allows for a high recycling ratio to be achieved at end of use.
In keeping with the goals of reducing embodied emissions, modular stainless-steel technology provides exciting opportunities to choose greener, more innovative solutions that can not only produce less emissions and waste, but also save time and costs for many councils in Australia.
If you’d like to learn more about Myrtha Pools and how modular technology could be used in an upcoming aquatics facility, please get in contact with david.bennison@mythapools.com or visit www.myrthapools.com.au.
Myrtha Pools is a GREEN STAR & LEED credited supplier.